CleanPump
Manuals
CleanPump
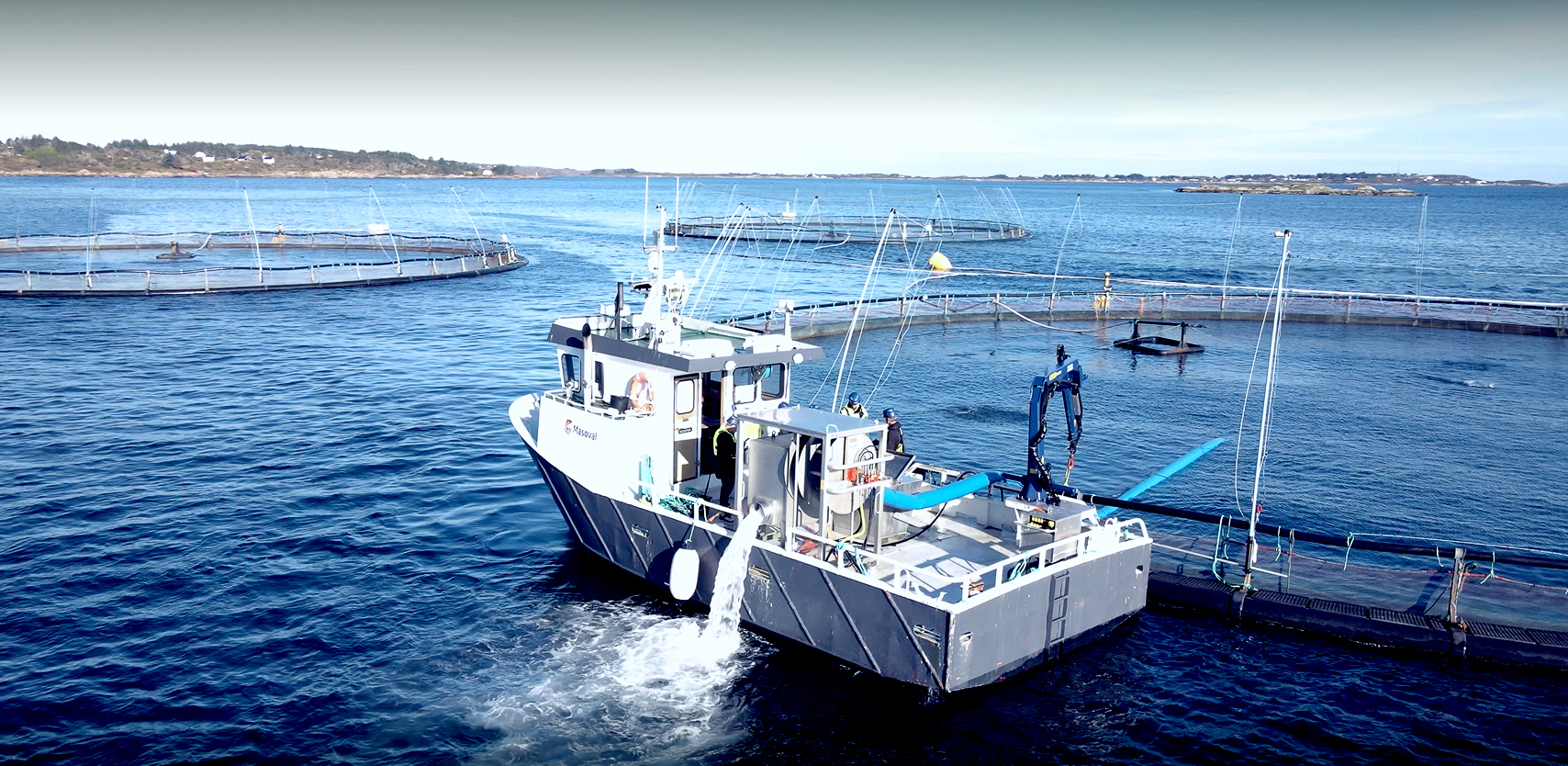
Innholdsfortegnelse
1. Purpose
This document is intended to provide the necessary information on installation, commissioning, use, maintenance, troubleshooting and disassembly.
1.1 Definition of product
Machine name: Servi CleanPump Gen. 3
Manufacturer’s reference: 784443 / 784443/10″
The product should not be used for anything other than what is specified in this document.
The purpose of the machine is to collect dead fish in cages through a hose using the venturi principle.
The machine is designed to be installed on board service vessels when removing dead fish from cages.
The machine is supplied with energy by connection to the vessel’s crane and supply of energy via pressure from the HPU of the crane. Control of energy supply must be done from the remote control of the crane or from the crane’s fixed control panel.
1.2 Manufacturer’s details
Scale Aquaculture AS, Nordfrøyveien 217, 7260 Sistranda, Norway | Tel: +47 73 80 99 30 Email: service@scaleaq.com Tel: +47 48 85 24 88 Email: support@scaleaq.com Website: www.scaleaq.com |
1.3 Technical information
Technical Specification: | |||
Max. operating pressure on port A/B | A/Bmax | bar | 250 |
Pump capacity A/B | l/min | 5 | |
Connections A/B | TEMA Series T, nipple 1/2″ | ||
Hoses A/B | 10 m | ||
Max pressure on port D | D max | bar | 3 |
Connections D | TEMA Series T, nipple 3/8″ | ||
Hose D | 10 m | ||
Weight species: 784443 Weight species: 784443/10″ | m | kg | 980 1035 |
Dimension LxHxW | mm | 2105 x 2180 x 1380 | |
Hydraulic fluid | Mineral oil for hydraulic system | ||
Viscosity (recommended): | v | m2/s | 32 to 46 (cST) |
Cleanliness requirements fluid: | ISO 4406 18/16/13 | ||
Temperature fluid: | T | -20°C to +50°C | |
Ambient temperature: | T | -20°C to +50°C | |
Pneumatic air hose dimension | 1″ (25 x 5.5) | ||
Pneumatic air hose length | 50 m | ||
Pneumatic air hose | Max. | bar | 15 |
Dead fish hose 8″ Dead fish hose 10″ | Flat blue, L =50 m |
Pneumatic air connection:
o Maximum allowable working pressure: 15 bar
o Pump capacity min: 2-3 m3/h @ 7 bar
Maximum traction drum: approx. 200 kg @ 200 bar
2. References
# | Servi doc no. | Title: |
1 | 2345570 | Assembly drawing art. 784443 (8″) |
2 | 2395886 | Hydraulic diagram art. 784443 (8″) |
3 | 2385759 | Assembly drawing art. 784443/10″ |
4 | 2395887 | Hydraulic diagram art. 784443/10″ |
5 | 2419311 | Declaration of Conformity |
3. Health, Safety and Environment (HSE)
3.1 General guidelines
- This machine should be installed according to this instruction before it can be used.
- Removing security elements or otherwise making changes or modifications that affect safety or functionality is strictly prohibited.
- Do not use the machine for any purpose other than its intended use.
- Installation or repair of the machine should only be performed by qualified personnel.
- All personnel operating the machine must have read and understood this manual.
- The limitations and instructions in this manual must be followed, especially those relating to safety.
- Serious injuries may occur if the machine is used for anything other than the intended use and if persons with insufficient knowledge operate the machine.
- Use caution when conducting lifting operations. Never remain under a suspended load.
- In addition to what is specified here, the safety rules of the local facility also apply.
- All warning signs must be in the same condition as it was when the machine was delivered. New signs can be ordered from the manufacturer if needed.
- Before operating the machine, ensure that all access to moving parts is prevented.
- All protection against moving parts must be permanently attached.
- Before cleaning, servicing or disassembling, disconnect hydraulic and pneumatic air connections.
- The machine has a high center of gravity. During transport, the machine must be properly secured in all directions to prevent tipping over. This can be done by strapping the machine to the floor or wall.
- Helmet and safety shoes/boots must be worn during machine installation/operation. For maintenance, safety glasses and gloves must also be worn.
- High pressure oil can penetrate skin, causing serious injury, poisoning and death. In case of injury, seek medical attention as soon as possible. Surgical intervention is required to remove oil.
- If hydraulic oil is swallowed/inhaled, seek medical advice. Do not induce vomiting if swallowed. Have safety data sheets for oil available.
- Fingers or bare skin should not be used to detect leakage. Avoid general contact with hydraulic oil.
- Locked hydraulic pressure before connecting and disconnecting or working.
3.2 Risk of escape
Use not in accordance with the manual may result in injury or hazard. It is therefore important that all equipment that is lowered into the cage cannot get caught, or otherwise cause damage to the net.
For assembly of vacuum funnel refer to section 7.2 of this manual.
Pulling force for the Servi CleanPump is limited to 200 kg to avoid equipment damage.
Care must be taken to ensure that the pulling force on the winch that pulls out the vacuum funnel does not become so great that it causes damage to the net. Winches that extract vacuum funnels are not part of Servi’s delivery, and their use falls outside Servi’s responsibility.
The use of a camera is recommended in connection with the extraction and retraction of the vacuum funnel, so that you can monitor that there is no risk of damage when using the Servi CleanPump.
4. Applications
CleanPump is intended for the removal of dead fish from aquaculture cages.
The machine has a hose coiled on the reel with a vacuum funnel at the end located at the bottom of the cage by means of an external winch. The vacuum funnel is then supplied with pneumatic air that creates the pumping effect. The dead fish come up through the hose in a stream of water and into a drainage box where the water is filtered off and the dead fish come out on a sorting table for counting. The dead fish then go into a vat for further processing.
The water is diverted out of the drainage box and guided overboard through a 12″ hose.
The drain hose is not part of the machine.
At the end of the pumping operation, the machine is supplied with hydraulic energy from the vessel crane and hoses for fish and air are rolled back onto the reel.
NOTE! | ||
Use of the CleanPump for purposes other than what is specified is prohibited. |
5.Description of the machine
5.1 Feature Description
See section 4
Main parts
The CleanPump consists of the following main parts:
- Frame
- Hydraulically powered hose reel
- Drainage box
- Vacuum funnel
- Fold-down sorting table
- Valve block
- Connection hoses
cf. Assembly drawing (see chapter 2).
All steel parts are manufactured from AISI316 acid-resistant steel for maximum corrosion resistance, except for the hose coupling for dead fish, which is made of aluminum.
5.2.1 Frame
The frame is manufactured from hollow profiles that carry the weight of the entire assembly. The frame has holes in the feet for attachment to the ground. The frame has lifting points in the upper edge equipped with 4 RUD VRS M12 lifting lugs which are to be used when the structure is to be lifted.
5.2.2 Hydraulically powered hose reel
Acid-resistant steel hose drum consists of 2 separate chambers respectively for roll-up of pneumatic air hose and dead fish hose.
The reel is driven by a hydraulic motor that also serves as a storage for the reel. The hoses are rolled out and pulled down in the center of the aquaculture cage with the help of a winch.
Winch for lowering is not part of this machine.
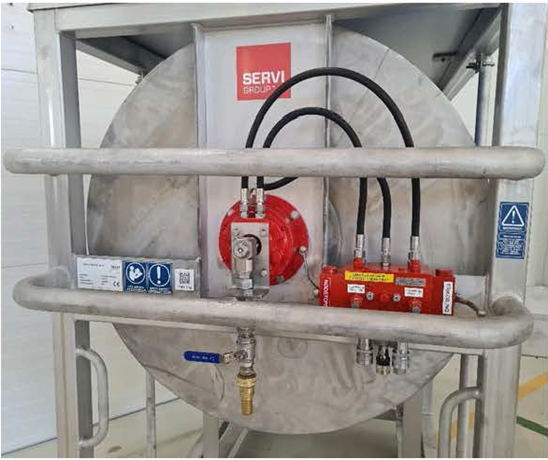
Figure 1 Hydraulic motor and connections
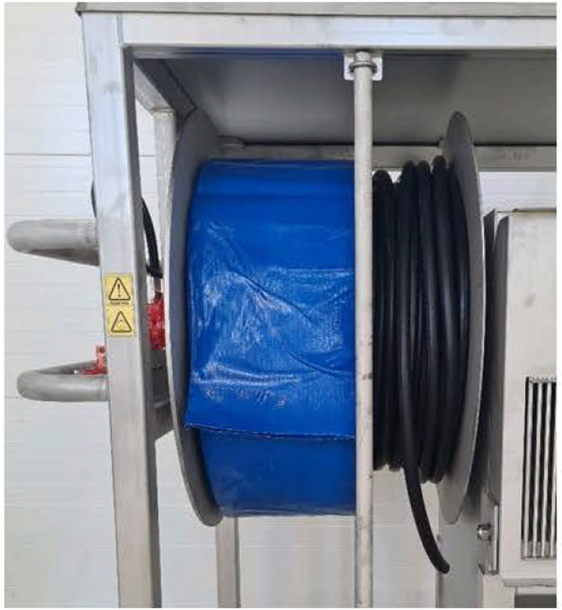
Figure 2 Hose reel
5.3 Drainage box
In the side of the drainage box, there is an opening for the inlet pipe for dead fish. A drain is fitted which can optionally be fitted to the side or rear, depending on the position of the machine on board the boat. In the cupboard, a strainer is fitted for quick removal of water and separation of dead fish.
Horizontal strainer can be removed without the use of tools for maintenance and cleaning the box
CAUTION! | |
Pinch hazard for fingers. Exercise care when handling horizontal strainer. |
5.3.1 Fold-down sorting table
The sorting table is fixed with hinges to the drainage box.
The table is used for control of the dead fish and as a slide for storage / further processing. When the machine is not in use, the table can be lifted and must then be secured with a lock.
NOTE! | ||
If the machine is moved/lifted, the sorting table MUST be folded up and secured. |
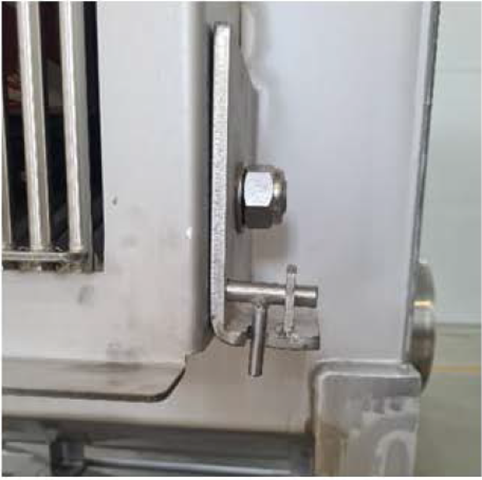
Figure 3 Lock on sorting table
6 Lifting and Handling
The machine must only be lifted using a crane and a 4 leg chain sling that is attached to 4 RUD VRS M12 lifting lugs on the frame. Check that the lifting lugs are securely fastened before lifting is carried out. Supplied lifting lugs must be checked regularly for deformation and corrosion by skilled personnel. Replace if necessary.
NOTE! | ||
The machine should be lifted only when empty, never with fish. The lifting lugs are not designed for anything other than the machine’s own weight. Always use all four lifting lugs when lifting |
Checklist before lifting and handling:
- Know the load limits. Do not overload crane, lifting equipment and moving equipment. Pay attention to the center of gravity of the equipment being lifted.
- Check that you have enough clearance over the object to be lifted.
- Check that lifting equipment to be used has valid certificates and is marked with the color of the year. Personnel must have sufficient training and be certified for lifting.
- Keep the work area clear. Remove clutter and unnecessary materials from the area. Do not allow personnel who are not directly involved in the moving operation to remain in the moving area
- Check the machine and accessories before the moving operation. Check for loose bolts, leaks, or other conditions that may affect the operation.
7 Installation
7.1 Mechanical Installation
CleanPump is supplied assembled from the manufacturer.
The vacuum funnel is delivered loose to the side due to saving space during transport and must be installed by the user before commissioning.
CleanPump can be lifted/moved into place as described in Chapter 6.
Ensure that the work area is free of loose objects.
Easy access to the control of the machine and a good distance to other elements should be ensured when placing CleanPump.
WARNING! | |
Risk of tipping. The machine’s center of gravity is relatively high. In the event of tilting and under stress from rolling in the hose, the machine can overturn. Proper attachment to the ground is therefore required. |
The machine should be secured to the ground by means of bolts on the feet.Use 4 M20 A4-70 grade bolts.If separate feet/pads are welded to the deck for this purpose, this must be done by trained personnel.
The machine should be secured to the ground by means of bolts on the feet.
Use 4 M20 A4-70 grade bolts.
If separate feet/pads are welded to the deck for this purpose, this must be done by trained personnel.
7.2 Installation of vacuum funnel
Flat hose is attached to the vacuum funnel using 2 hose clamps that are included.
2 x hose clamps are threaded into air hose before threading into the brass fitting. Screw clamps are tightened over the brass nipple. Make sure the screw on the hose clamp faces the vacuum funnel.
Use the supplied tape to cover the spigot and hose clamps for the air hose. Flat hose clamps are covered in a similar manner. It is recommended that the air hose is taped to the vacuum funnel together with hose clamps for the flat hose.
. | WARNING! |
Risk of damage to the net. Sharp edges on the vacuum funnels and associated equipment that are lowered into cages can get stuck and cause the net to be damaged. Proper taping is required to avoid damage. |
7.3 Hydraulic connection
The system must be connected to a free hydraulic outlet on the crane, with pressure and return hose respectively via 1/2″ quick coupler.
CAUTION! | |
Slip hazard in the event of oil spillage on deck. In the event of oil leakage on deck, it can become very slippery, especially in combination with water. Stop operation and dry up oil spills immediately. |
NOTE! | ||
Requirement for emergency stop. The crane’s remote control and/or the crane’s permanently mounted control panel must have an emergency stop that shuts off all the supply of power on the hydraulic circuit to CleanPump. |
All hydraulic hoses must be securely fastened so that they are not in the way. This is also important in order to avoid unnecessary wear and tear. When unloading and loading pressure, some movement in the hoses should be expected.
- Air connection
The machine is connected to air via air quick couplers located on the air hose reel.
WARNING! | |
Danger of whipping and strikes. If the air hose breaks, this can cause the end of the air hose to strike and whip with great force. Safety cables must therefore be installed on all air hose connections. |
7.5 Lighting
The machine is delivered without its own lighting. Do not operate the machine unless it, and the surrounding area, is adequately lit.
7.6 Arrival
The machine is designed to be placed on the open deck. Operational handles and connections are located on the left side seen from the front. The service area for CleanPump is indicated in the assembly drawing.
cf. Assembly drawing (see Chapter 2).
7.7 Commissioning
The checkpoints below should be reviewed each time the machine is installed on a vessel.
Before connecting:
• Check that the machine is intact and undamaged.
• Check that the machine is properly secured to the ground. See also Chapter 7.1.
• Check that all moving parts have unhindered movement.
After connection:
• Perform the maintenance items for monthly maintenance, see Chapter 10.3.
• Check the direction of rotation of the hydraulic motor. This is done by starting it for a short time and checking the direction of rotation of the reel. If the reel goes the wrong way, the direction can be easily changed by switching the A and B connections.
• Check that the emergency stop valve works by starting the reel and then shutting the emergency stop valve. Check that the reel stops. During normal operation, this valve is left open.
• Check that the reel runs smoothly and without noise. See also Chapter 9 for troubleshooting.
If the machine is not used for a period of time:
• After receiving the machine, it must be connected to the hydraulic system, and the reel must run for 5 minutes each way, if the machine is not used within 3 months.
• Then run every 3 months as long as it is not in use.
• During the maintenance run, it is necessary to secure the flat hose and air hose so that it is not damaged during the run.
• Flat hose and air hose are inspected for damage in connection with maintenance run.
• If the hoses are dropped into salt water during a maintenance run, these must be flushed with fresh water during coiling before the machine is put away for further storage.
8 Operation guide and function description
• The vacuum funnel attaches to drop-down rope that runs via bottom in cage to drop-down winch.
• Open the release valve to set the hydraulic motor to free run.
• Draw the dead fish hose into the cage using the drop-down winch.
• Connect air hose to compressor.
• Start the air compressor to initiate pump operation. Check that plenty of water comes out of the pipe for dead fish inside the drainage box.
If this does not happen, move on to troubleshooting. See also Chapter 9.
NOTE! | ||
If the reel has a higher speed than desired when the release valve is open, throttle the release valve carefully. This will slow down the reel. |
NOTE! | ||
The person controlling the machine through the handheld remote control or the control panel of the boat crane has primary responsibility during operation. This person must keep an eye on all moving parts and be in control of all situations. The person in question is responsible for the safety of personnel participating in the operation or in the machine work area. The person in question must be positioned to have an overview of the entire machine and the operation, as well as access to the manual control valves on the machine. The person who controls the machine must be sober and not under the influence of drugs or medicines. |
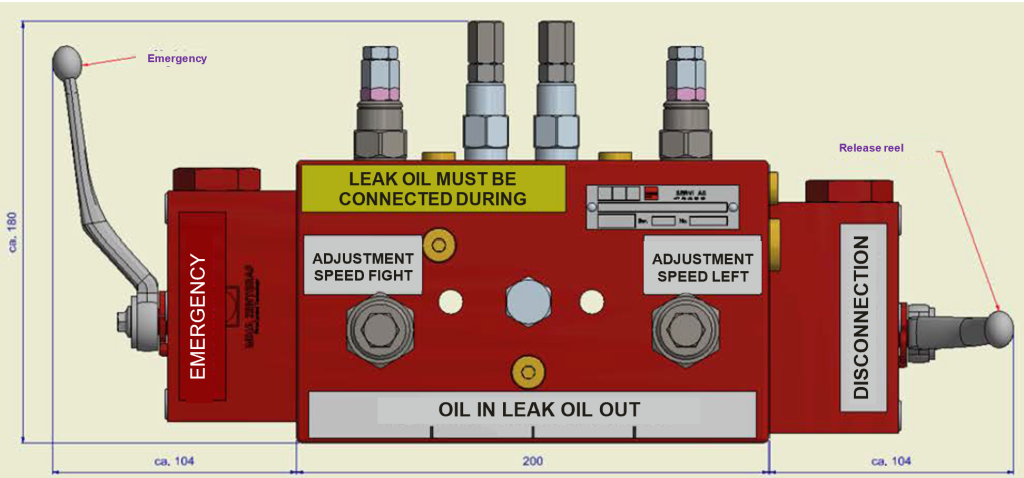
After use:
• Use the reel to pull hose up from the cage. The drop-down winch must be fed with a rope.
• Monitor reeling of dead fish hose and air hose. Stop reeling and correct if necessary.
• Check that the pump hose is emptied of water as best as possible before it is rolled onto the reel.
• Check drainage box and clean if necessary. See chapter 10.2.
• Fold up the sorting table and secure it with a lock.
WARNING! | |
Risk of entrapment of limbs, tearing. The machine draws in the hoses with high force – up to 200 kg. If you have to correct the hoses due to crooked reeling, this must be done at a good distance from the machine so that you do not risk getting pinched. If you continue to have issues with crooked reeling of hoses, you should consider a permanent measure, e.g. in the form of steering rollers on the boat railing. NB! Remember that the operator of the remote control or control panel controlling the power supply to the machine is responsible for monitoring and immediately stopping the operation if a potentially hazardous situation occurs. |
WARNING! | |
Risk of coils/loops on hoses. Air hose and vacuum hose may be pulled at slightly different speeds. This may cause air hose to coil slightly on deck. Both when pulling out and pulling in hoses, you must exercise care and not step on coils. Crushing injuries can occur and you can be pulled over. |
9. Abnormal events/errors
Errors that may occur during use, with possible causes.
If you are unable to correct errors yourself, contact SERVIAS for further assistance.
9.1 The reel
The reel does not move or moves slowly.
- Check that the emergency stop valve is open and the release valve is closed.
- Check that all hydraulic couplings are connected.
- External pump does not have sufficient capacity.
- External winch resists (when reeling in).
9.2 Pump function
Not enough water comes out of the top.
- Insufficient air supply. Check connections.
- Not enough capacity in the compressor.
- Leakage or blockage in air or pump hose.
- The air hose must be completely reeled out from the reel. If the air hose is left on the reel when vacuum hose is completely out, it will reduce the air supply greatly and, in the worst case, completely.
9.3 Net lifting at start-up
If the net is lifted and blocks use of the machine, the weight of the load weights must be considered to be increased.
10. Maintenance
10.1 Safety
NOTE! | ||
For all service, the safety measures in Chapter 3 must be adhered to. Conducting service and maintenance work on the machine while it is in operation is prohibited. Connecting the machine for the duration of installation, maintenance or other work on the machine is prohibited. If the dead fish hose is dismantled while most of the hose is out into the sea, the hose must be secured/attached so that the entire hose is not drawn into the sea. |
10.2 Cleaning
- Lift out the grate in the drainage box (can be done without tools).
- Flush the inside of the enclosure and strainer with high pressure washers.
- Wash the exterior of the machine with high pressure washers.
- Use caution when washing down hydraulic components.
CAUTION! | |
Pinch hazard. Exercise care when handling grating. |
1.3 List of checks and their intervals
Control/Check | Daily, before start-up | Weekly | Monthly | Annually |
Check operation of the emergency stop valve. | X | X | X | X |
Check operation of the release valve. | X | X | X | X |
Check quick couplers for leaks. | X | X | X | X |
Check vacuum funnel for damage. | X | X | X | X |
Check that vacuum funnel hose clamps are covered with tape to prevent damage to the cage. | X | X | X | X |
Check that no oil leaks from hydraulic motor, valves and couplings. | X | X | X | X |
Check against mechanical damage, that the frame, reel, drainage box and sorting table are complete and undamaged. | X | X | X | |
Check that the reel runs evenly | X | X | X | |
Unroll the hoses and check thoroughly for wear and damage. | X | X | X | |
Check that screws and bolts are tight. Tighten if necessary. | X | X | X | |
Check machine movement. Check that there is no slack in the reel. | X | X | ||
Check that all signs are in place. Replace if necessary. | X | X | ||
The hydraulic motor is checked for slack or noise. | X | |||
Check for corrosion on stainless steel parts. | X | |||
Check hydraulic motor surface treatment, components and associated equipment. Repair any damage. | X |
11 Replacement parts and repairs
Some replacement parts may have a long delivery time, and the machine owner should consider the consequences of any downtime and order critical parts for storage.
Mechanical damage to the reel or frame can be repaired by a qualified mechanical workshop.
In the event of faultiness with the hydraulic system or hydraulic components, contact Servi AS.
12 Destruction/disposal
The machine is cleaned and all residues of biomass are removed.
Drain oil from machine components and remove residual grease.
Disassemble the machine and send the different components to the appropriate recycling sites:
- Oils and lubricants.
- Steel construction and metal parts.
- Any residual waste that remains.
Any disposal in the form of resale for continued use requires that the seller also send the machine’s associated documentation to the new owner.
13 Appendix
- Assembly drawings
- Hydraulic diagram
- Overview of Servi CleanPump sign
- Hydraulic Motor Data Sheet
- Declaration of Conformity